■幸町工場の思い出 New!
(事務局付記) 当ホームページ3月号で長崎造船所幸町工場の全ての生産機能を他の拠点に移すという重工ニュースをお伝えしました。ここでは
長年舵取り機やタイヤ機械を担当された幸工OB海田秋男様から思い出を綴った投稿を頂きました(相馬和夫様経由)ので
掲載いたし ます。(事務局)
○海田秋男様(幸工OB 特別寄稿)
(1) まえがき
幸町工作課と私の関わりは技術学校卒業後の昭和37年4月当時の第2機械工場一工作係(幸工課の前身)に配属されてから始まります。当初同じ一工作係に配属された同僚の金子君と私は1年間の教育期間を与えられ過給機組立作業班の中島組に預けられます。中島組での実習作業は機械加工部品のカエリとりやケーシングジャケット内に残留した鋳物砂の砂落としが主な私達の教育課題でした。この中でも砂落とし作業ではかなり苦労した覚えがあります。
その後、職場生活にも慣れたころ、教育期間の1年も過ぎ私は正式に舵取機組立班の金子組に配属される事になりました。私の本格的な幸工課との関わりはこれよりスタートする事になります。
昭和38年4月金子組の舵取機を皮切りに、昭和43年に新規導入されたゴムタイヤ機械の加硫機、成形機、インターナルミキサーを主流とした生産機の総合組立、工場内調整運転、現地工事などが私に課せられた幸工前半期の仕事でした。その中で過去を改めて振り返るとこの前半期に体験した挫折感や達成感が私の思い出となって沸沸と蘇って来ます。
後半期は、現場を離れ、組立係、企画係、課直の仕事に携わりますが平成10年出向により幸工課を去りました。この間在籍36年間の中で特に私自身の仕事の転機となったタイヤ加硫機(初号機)の思い出について次に記したいと思います。
(2) タイヤ加硫機(初号機)の思い出
昭和43年米国NRM社との技術提携によりタイヤ生産機械の中でも最大の量産機種であるタイヤ加硫機を幸町工作課が担当する事になった。この事は幸町工作課にとって今後の工事量を確保する命題であり事前の備えが不可欠であった。
これによる幸工課の対応策は次の案件だったと記憶している。
1)組立作業班の人員構成見直 (若手を起用した構成替え) (組立)
2)勉強会の開催(定時後、若手を集め実施) (組立)
3)加工治具の事前製作(量産部品への対応) (生技)
4)溶接用ポジショナーの導入 (製缶)
5)小型ボイラー設備導入 (組立)
6)冷嵌め用フリーザーの導入 (組立)
7)制御回路図(シーケンス)の事前検討 (組立)
以上の備えを進める中、横浜ゴム殿向タイヤ加硫機(20台)が正式に受注される事になる。当時、私も25~26才の年齢に達し組立作業の経験やタイヤ勉強会の予備知識を背景として多少の自信はもっていたが、いざ実践となると一抹の不安は少なからず有った。その後本工事の納期を左右する設計課の出図日程は予定どおりとなり必然的に幸工課企画係の処理業務も活発化する事になる。
さらに製缶用の材料手配や加工外注メーカーへの発注などが同時進行する。今回のタイヤ加硫機は初号機と云うこともあり大物部品のベース溶接やビーム溶接は製缶工事から機械加工まで内作によって成品化される計画となった。従って、私共、組立班にとっては大物部品の進捗状況を観察出来る様になり組立工程の段取りも楽になったと思われたが組立作業の開始条件として一番重要な部品チェックに於いて問題が発生した。この作業は部品表を基準に入荷の有無を確認し、手持ちの部品表に員数チェック後マーキングするという単純作業であったが本オーダーでは部品表の内容と納入品に付けられた荷札に不備があり、部品の照合作業が出来ないという不具合が発生した。原因は部品表が英文作成であった事や荷札の書き方が統一されてなかった等の事由によるものであったがこの件は部品表の見直しと統一された荷札に変えると、設計より回答された為に当面は単品製作図を発行する事で一応の解決を得た。
一方、大物部品のベースとビームの加工品は予定通り完成し組立現場へ搬入され本格的な組立作業の開始となった。サブアッシーのベース組立・ビーム組立に於いては事前検討の成果も有り小さな問題を除き全体的には無難に進捗した。最終工程のベース組立本体にビーム組立品を一体化する総合組立についても予定通りの工法で無事完了する事が出来た。
加硫機の全体の骨格が完成すると残るは小物取付と配線・配管工事のみの作業となり物理的工事はほぼ終了する事になるが配線・配管については幸工課常駐の協力会社が施工する事になっており私達は次に控える運転調整の準備に取り掛かった。しかしこの作業の具体的な進め方を示すマニュアルやチェックシートなどの手引書なる物は存在せず、何から手を付けていいのか途方に暮れている時貴重な大先輩がいることを知らされた。この方は、NRⅯ社と技術提携後、NRⅯ社のアクロン工場を幸工課代表として工場視察団に参画された人であった。更に私達の大先輩でもあり「渡りに船」の思いで手ほどきを受ける事になる。大先輩より指導を受けた調整手順の内容は以下の通りであった。
▷手順 1)モーター付減速機内へ潤滑油を充塡する
2)高圧グリスポンプのタンクへ規定のグリスを充塡する
3)高圧グリスポンプを作動させ摺勤各部へ給油しているか
端末のチューブを外してグリスが出てくる事をチェックする
4)締付力テスト(仮操作盤・仮モールド代用品の要準備)
電流・電圧・締付トルク(規定どおりの数値になるまで調整)
5)ビーム本体の動作をコントロールするロータリーカムスイッチのセット
6)検出リミットスイッチの設定
7)手動運転
8)自動運転(加硫タイマーの動作確認)
9)社内検査
10)客先立会
11)発送準備→出荷前検査→現地発送
この手順に従い1項目づつの作業に挑戦していくことになるが、この調整作業の中で特に難解だったのは
手順4)締付力テスト
手順5)ロータリーカムスイッチのセット
手順8)自動運転(加硫タイマーの動作確認)
この3項目の作業に悩まされた事です。運転調整の最終手段に当る自動運転では加硫タイマーの動作に異常があり原因を調査するも分らず、とうとう一夜を明かす羽目になったなど初号機にまつわる失敗談の思い出は語り尽くせないものがありました。そしてこの初号機も紆余曲折の末、完成の暁を迎えますがこの加硫機で学んだ知識と技術そして粘りはその後の成形機・インターナルミキサやOTRプラントへと繋がり大いに貢献したと自負しているところです。
(3) あとがき
幸町工作課の思い出を綴るに当り過去を取り戻したく、幸工課を訪問した。新任課長の荒木課長の計らいで私のタイヤ機械時代の戦友でもある池松社員を相方に付けてもらい大いに助かりました。彼の案内で工場周辺を散策したが回りの風景は南伸道路の建設に伴い様変わりした感じは受けましたがよくよく見ると被爆当時の形跡は未だ至るところに散在し懐かしくもあり淋しくもあった。
私の20代前半頃「ハウスキーピング」という社内的取組みがあり18棟の組立場に全員で横列に並びタバコの吸い殻拾いをやらされた頃を思い出すと苦笑しかないが一方では当時の日本の後進性を裏付ける証しとも云えます。その当時は更衣所も食堂もなくすべて現場に持ち込んで処理するのが当り前の時代でした。現在とは格段の差を感じるが、さて、どちらが良いのかと問われれば私は昔を採る気がします。やはり知力・体力・気力に勝る若い頃の力は失敗・成功の区別なく人生の尊い思い出となり誰もがもつ財産であると私は信じて疑いません。
以上、幸町工作課を改めて振り返る機会を与えて下さった関係者の方や作成に御協力戴いた方々に心より感謝申し上げ筆をおきたいと存じます。
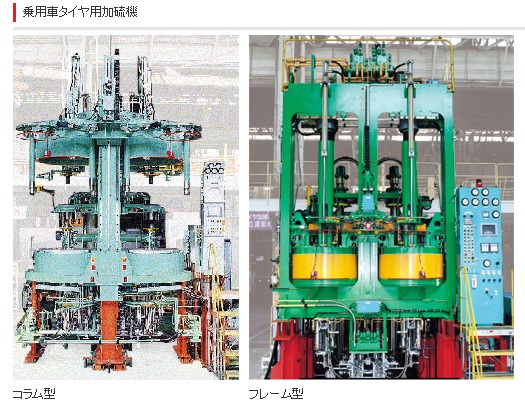
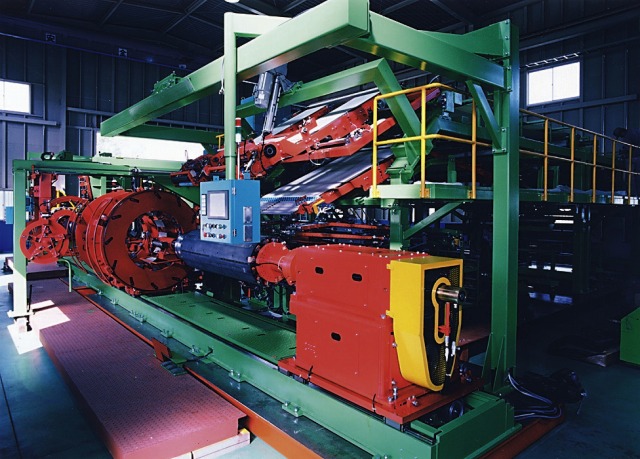
三菱重工マシナリーテクノロジーの
ホームページより
昭和44年の1号機以来、加硫機3,000台、成形機700台と記載あり